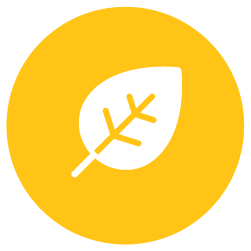
CONTROLLED EMISSIONS
TODAY’S MODERN PLANT
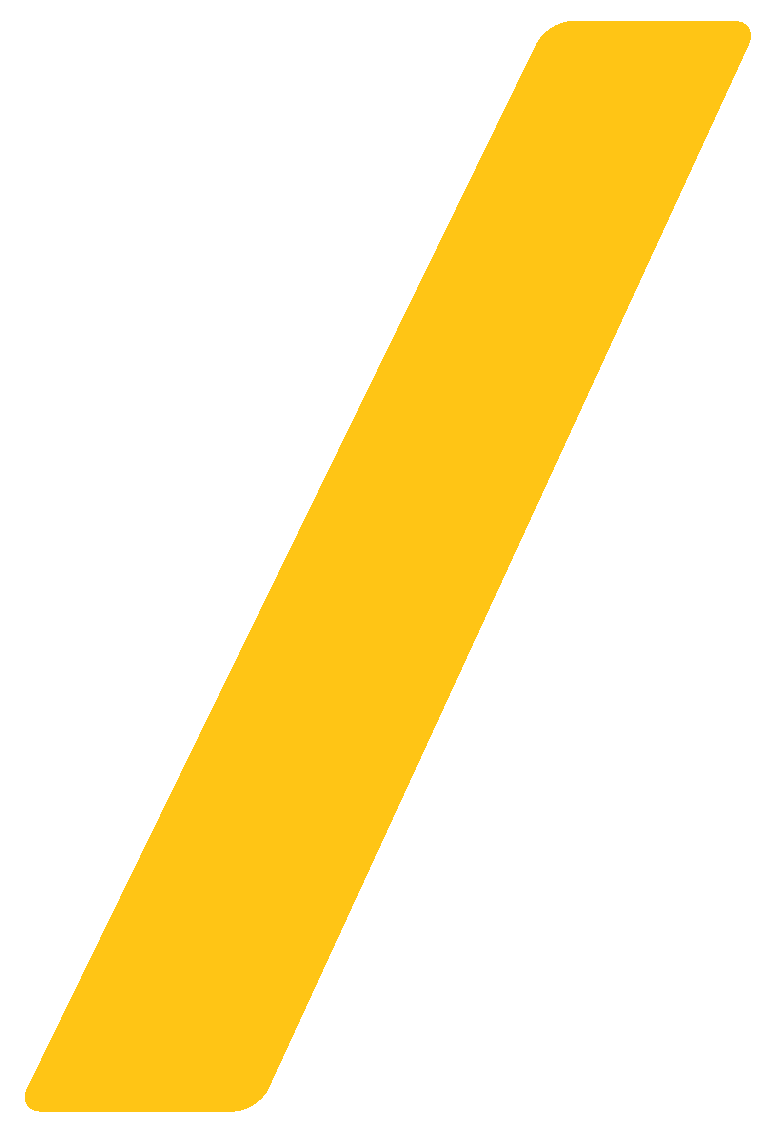
Another major change has been the implementation of the baghouse, a filtration system to collect any dust produced while the aggregate is being heated and keep it out of the air. In fact, the dust produced during this process is collected and stored on site to be used at the appropriate percentage based on the mix design. Research is constantly being conducted on new ways technology can be used to make plants more efficient and safer than ever before.
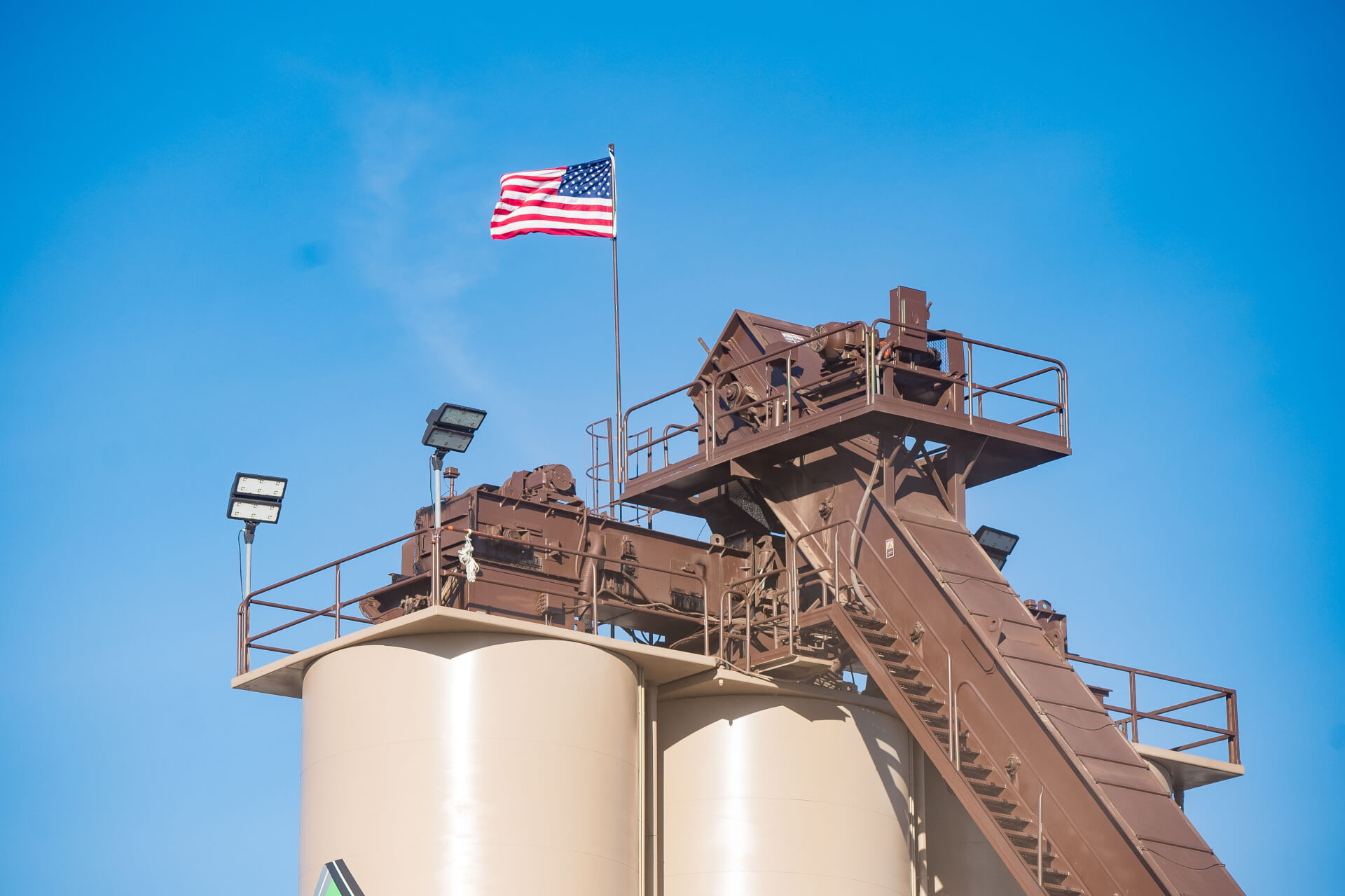
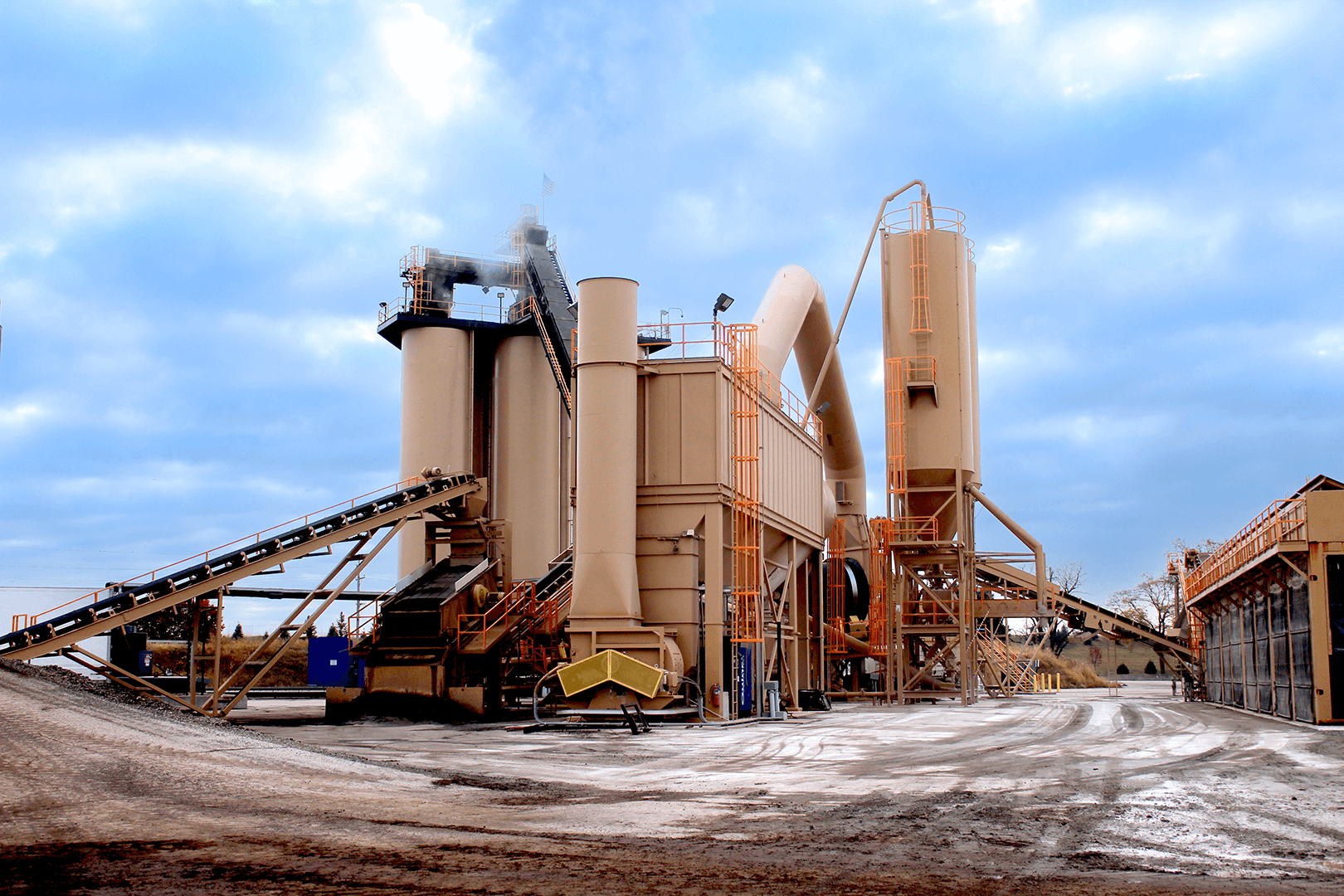
Steam, Not Smoke
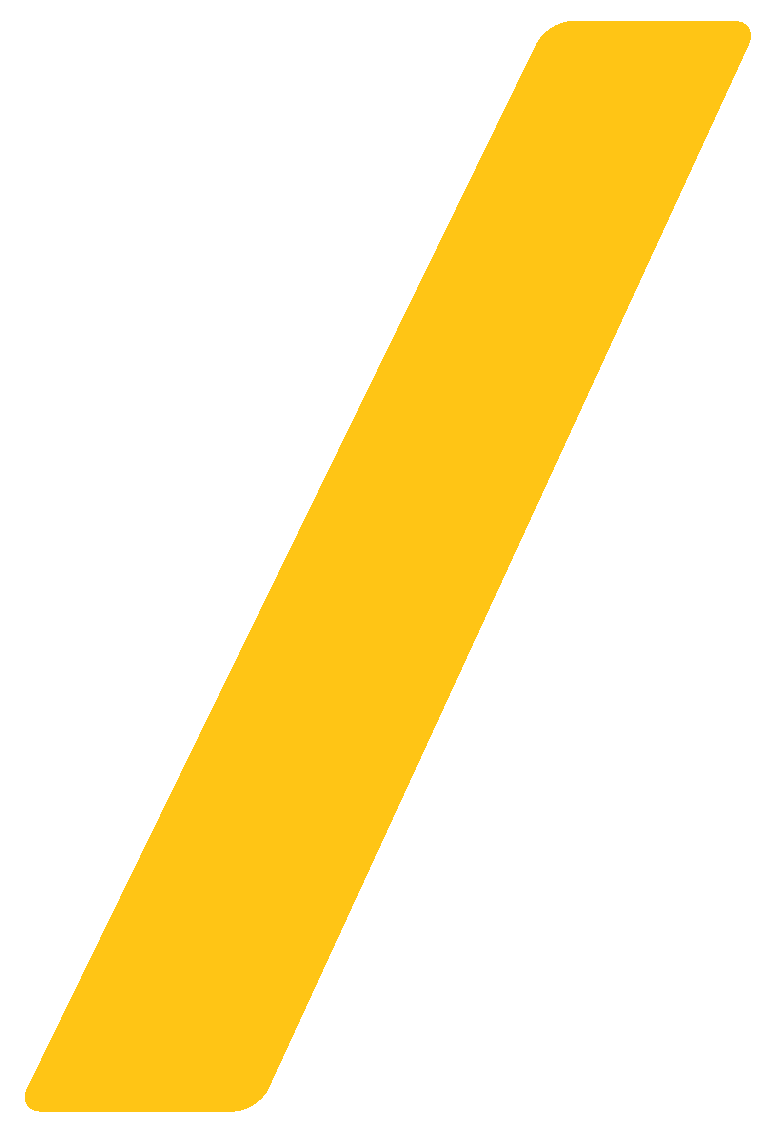
When driving past an asphalt plant you may see what appears to be smoke coming from a stack, but what you are actually seeing is steam. As part of the asphalt manufacturing process, aggregate is put into a drum to be indirectly heated and prepared for the binder to be added. During this heating process the aggregate loses its moisture in the form of steam. That steam is then vented out to ensure the aggregate is dry. The dry aggregate is then combined with asphalt binder to produce safe and high quality asphalt pavement.
RETHINK EMISSIONS
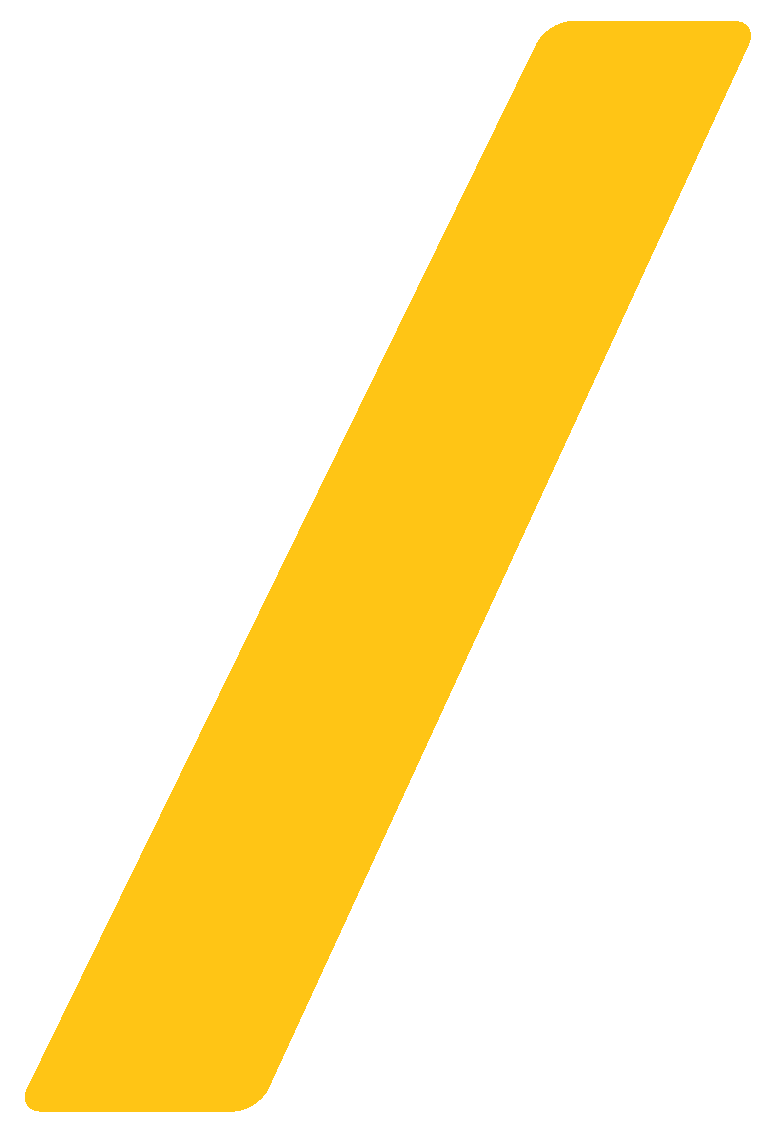
Driving down a street lined with fast food chains, one’s mind does not instantly go to “What they are emitting?” the same way it could when seeing a production plant. However, when comparing the amount of particulate matter (solids and liquids in the air) produced during asphalt production, it’s the same as just two fast food restaurants. Another form of emissions that is tightly controlled & regulated are VOCs or volatile organic compounds. These are gasses that are emitted into the air from products or production processes that can irritate the eyes, nose, and throat, among other symptoms. It might be surprising to learn that an asphalt production plant produces only 1/12th the amount of VOCs as an average bakery.
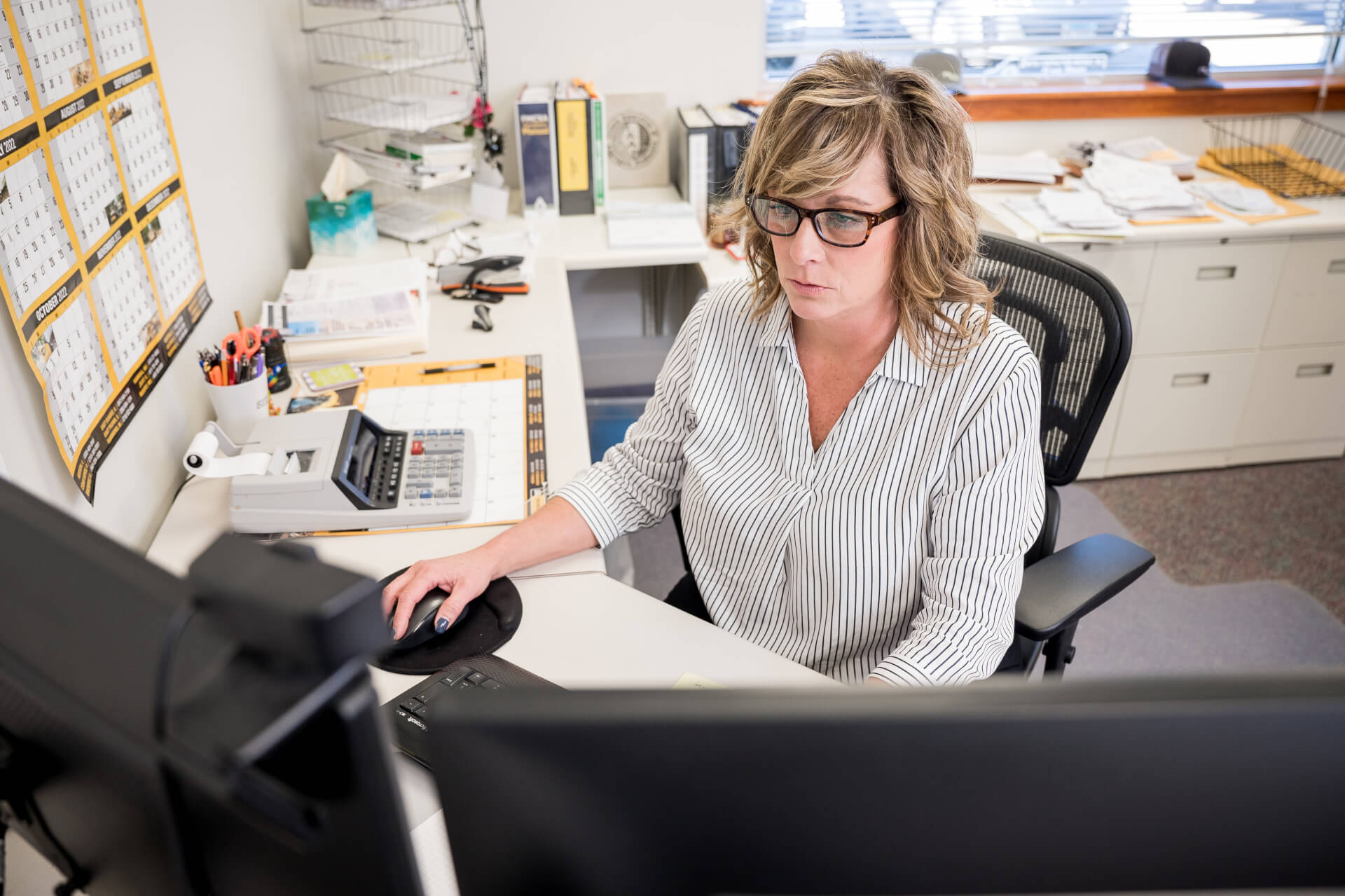
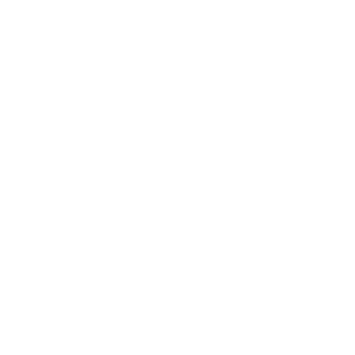
RECYCLING
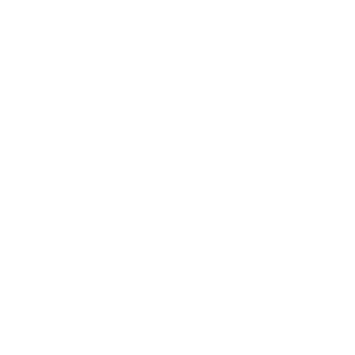
Safe And Smooth
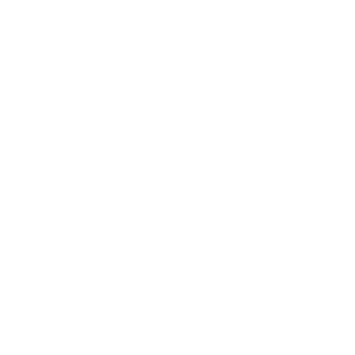
GOOD NEIGHBORS
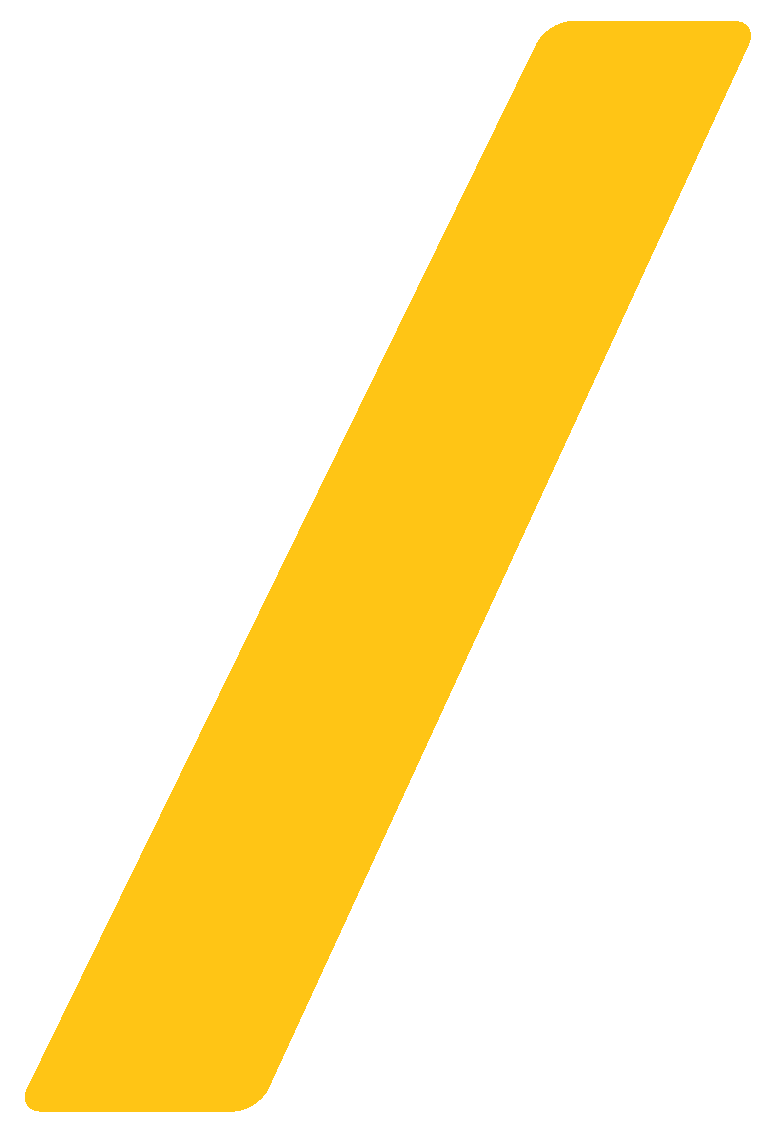
More
Resources
Looking for additional information? Please visit our resources page for access to the articles and organizations referenced on this site, as well as some helpful definitions for industry specific terms.